Win at Work with 5S – Learn How!
Looking to boost productivity and efficiency in your workplace? Consider the 5S method! This system has revolutionized workplaces globally, streamlining processes and creating a safer, more organized environment for employees.
In this article, we’ll explore the 5S method and learn how to implement it in your own workplace for success. Say goodbye to clutter and chaos, and hello to a more productive work environment with 5S!
Understanding the 5S Methodology
The Origin of 5S: A Look at the Japanese Phrases
The 5S methodology consists of five Japanese phrases: Sort, Set in Order, Shine, Standardize, and Sustain. In English, these phrases represent distinct steps in workplace organization and efficiency.
The Japanese origins contribute to the unique history and understanding of the 5S framework, showcasing its roots in post-war Japan and its subsequent international prominence through companies like Toyota.
In the implementation and maintenance of a 5S system, these Japanese phrases play a crucial role in guiding the step-by-step process of organizing the workplace, ensuring cleanliness and standardization, and sustaining these changes over time.
The phrases serve as a practical and general framework for companies across industries, allowing them to improve efficiency and reduce waste in their business processes.
The Japanese phrases encompass the core principles of 5S and serve as the foundation for successful implementation and maintenance in the workplace.
The 5S Framework Explained in English Terms
The 5S framework has five steps:
- Sort.
- Set in Order.
- Shine.
- Standardize.
- Sustain
These steps focus on organizing the workplace, ensuring cleanliness, and maintaining standardized processes.
In manufacturing, the 5S framework enhances efficiency by creating a systematic and organized work environment. It reduces waste, improves productivity, and promotes a safer workplace, ultimately leading to cost savings and increased quality.
Various workplaces such as manufacturing plants, healthcare facilities, construction sites, and hospitality businesses have successfully implemented the 5S framework. Companies like HP, Boeing, and Nike have effectively utilized the 5S methodology to streamline their operations and improve overall efficiency. The 5S framework has also been widely adopted in lean manufacturing principles and has proven to be an integral part of the Toyota Production System, showcasing its versatility and impact across different industries.
The Crucial Role of 5S in Enhancing Manufacturing Efficiency
The 5S methodology in manufacturing has many benefits:
- It reduces waste, improves productivity, and creates a safer work environment.
- It eliminates unnecessary tools and materials, streamlining processes and reducing costs.
- An organized workspace leads to fewer accidents and injuries, enhancing overall safety.
- Efficient workflows and standardized processes ensure consistent product quality and output.
- It also promotes employee engagement and ownership of the workspace, resulting in a more motivated and empowered workforce.
The 5S methodology enhances manufacturing efficiency by promoting workplace organization and cleanliness through these steps:
- Sort.
- Set in Order.
- Shine.
- Standardize.
- Sustain
These steps help eliminate wasted time, reduce the risk of equipment breakdowns, and maintain a visually controlled environment, leading to improved operational efficiency, increased equipment reliability, and reduced downtime.
An organized work environment enables employees to focus on value-added tasks, enhancing overall productivity.
To maintain 5S standards over time, it is important for companies to:
- Provide ongoing training and certification
- Educate employees on the 5S methodology
- Create a visual workplace using tools like shadow boards and floor markings
- Continuously monitor and audit 5S practices to identify and address areas for improvement, ensuring long-term success and effectiveness.
Top Five Advantages of Implementing a 5S System at Work
Implementing a 5S system at work offers many advantages:
- Waste reduction
- Improved productivity
- Safer workplace
- Enhanced efficiency
It contributes to manufacturing efficiency by optimizing workflow and reducing unnecessary downtime.
Additionally, 5S implementation ensures a safe work environment by promoting cleanliness and organization, thereby minimizing the risk of accidents and injuries.
Step 1: Sort (Seiri)
Definition of Sort and Its Workplace Necessity
The “Sort” step in the 5S methodology means removing unnecessary items from the workplace and keeping only the tools and materials you really need. This creates a more organized and efficient environment, cutting down on clutter and making processes smoother.
“Sort” helps with workplace efficiency and organization. It makes it easier for employees to find what they need, saving time and cutting out errors. This improves quality and productivity.
Real-life examples of “Sort” working well include manufacturing companies, where production flow improved and downtime reduced. Healthcare facilities also saw better patient care with more organized and accessible medical supplies. Offices and service industries got a boost in employee productivity and customer service through “Sort.”
Best Practices for Sorting in the Workplace
The 5S methodology guides best practices for workplace sorting. It involves removing unnecessary items to create a clean and organized work environment. This includes identifying and disposing of items no longer needed, organizing essential items for easy access, and creating designated storage spaces. Sorting boosts overall efficiency and organization by reducing clutter, minimizing time spent searching for tools or equipment, and streamlining workflow processes.
Real-life examples of successful sorting in the workplace using the 5S method can be seen in manufacturing facilities. There, tools and materials are systematically arranged for quick retrieval. In healthcare settings, supplies are organized to optimize patient care. The 5S methodology has been widely adopted across various industries, such as construction, hospitality, and healthcare. It has led to significant improvements in productivity and workplace organization.
Real-life Implementations of Sort
The “Sort” step in the 5S methodology has made workplaces more efficient in real-life situations. By tidying up workspaces, companies have made it easier for employees to find tools, materials, and information. This has reduced downtime and increased productivity, as employees spend less time looking for items and more time on their tasks. The “Sort” step has also led to waste reduction, saving companies money.
Big companies like Toyota, Boeing, and Nike have used the 5S methodology to improve production. By implementing the “Sort” step, they have seen improved workflow, less waste, and happier employees. Healthcare facilities and construction companies have also used the “Sort” step to organize their spaces and create a more efficient and safer environment for their staff.
The “Sort” step has helped create a safer work environment by reducing clutter and improving organization. In manufacturing, removing unnecessary tools and materials has lowered the risk of accidents and injuries. In healthcare, it has led to better organization of supplies, reducing errors and accidents.
Step 2: Set in Order (Seiton)
Explanation of Set in Order and Its Importance
The Set in Order step in the 5S methodology is important. It focuses on organizing the workplace to maximize efficiency. By arranging tools, equipment, and materials logically, employees can find what they need easily. This reduces time wasted searching for items and streamlines processes. Proper implementation of Set in Order can also improve safety by keeping work areas free from clutter and obstructions. This reduces the risk of accidents and injuries.
Creating a more organized and efficientwork environment enhances productivity, quality, and overall employee satisfaction. Understanding Set in Order and its implementation is important for organizations. It directly impacts operational performance and cost-effectiveness. Effective workplace organization and layout contribute to a more streamlined workflow, reduce waste, and improve overall efficiency.
Therefore, organizations need to prioritize proper implementation of Set in Order to create a safer, more productive work environment.
Strategies for Organizing Workspace with Seiton
Organizing your workspace with the Seiton (Set in Order) step of the 5S methodology involves a few effective strategies:
- Arrange tools and equipment ergonomically and accessibly.
- Label items for easy identification.
- Use color coding for visual management.
- Define specific locations for items.
This step helps to create a more efficient and productive work environment by reducing unnecessary movement and search time. It optimizes workflow and improves productivity.
To maintain this organization, it’s best to:
- Conduct regular audits.
- Train employees on workspace arrangement.
- Involve all team members in upkeep.
- Continuously review and refine the workspace layout to accommodate changes.
Step 3: Shine (Seiso)
What Does Shine Mean and Its Significance?
The principle of “shine” in the 5S methodology means keeping the workplace clean and organized. This includes regular cleaning, maintenance, and making sure equipment and work areas are free from debris, dirt, and hazards.
In the context of the 5S framework, “shine” is important because it helps maintain cleanliness and organization, which are vital for efficiency and safety. When the workplace is clean and orderly, employees can easily find tools and equipment, spot potential issues like spills or leaks, and ensure a safe working environment.
Procedure for Ensuring Workplace Cleanliness
In the 5S methodology, it’s important to establish specific procedures for workplace cleanliness. This includes setting guidelines for regular cleaning schedules, designated cleaning areas, and proper waste disposal methods, as part of the ‘Shine’ aspect of 5S. For example, companies can institute daily cleaning routines, like wiping down workstations, organizing tools and materials, and ensuring equipment is free from dust and debris.
Maintaining workplace cleanliness not only keeps the surroundings looking good but also improves efficiency and safety. To sustain 5S standards, organizations can monitor workplace cleanliness through routine audits, ongoing staff training, and fostering a culture of accountability for maintaining a tidy workspace.
Real-life examples of the ‘Shine’ step include regular cleaning and equipment maintenance, such as cleaning and lubricating machinery, and keeping work areas free from hazards. These proactive measures lead to a safe and organized workplace, aligning with the 5S methodology.
Illustrative Cases of Shine in Action
Businesses have been successful in implementing the “Shine” (Seiso) step of the 5S methodology. They do this by including regular cleaning and maintenance practices in their daily operations.
For instance, manufacturing facilities make sure to keep machines, equipment, and workspaces in great condition by cleaning and inspecting them regularly. This has led to significant improvements in workplace efficiency and safety.
By embracing the “Shine” (Seiso) step, companies have seen less downtime from equipment failure and fewer workplace accidents caused by faulty or dirty machinery.
Additionally, the “Shine” (Seiso) step is crucial for maintaining a safe work environment within the 5S framework. It promotes cleanliness, order, and proper maintenance of tools and equipment. This helps prevent accidents, injuries, and potential hazards in the workplace, making it a safer and more productive environment for employees.
Step 4: Standardize (Seiketsu)
Understanding Standardization and Its Workplace Role
Standardization in the workplace contributes to operational efficiency. It creates uniformity and consistency in processes and procedures. This helps organizations streamline workflows, reduce errors, and minimize waste. It ultimately leads to improved productivity and cost savings.
Standardization also plays a role in maintaining a safe work environment and improving workplace organization. Best practices are consistently applied, leading to reduced safety hazards, clear workspaces, and improved overall cleanliness.
In different industries, effective standardization practices have led to significant benefits. For instance, in manufacturing, standardizing equipment maintenance schedules has reduced downtime and improved equipment reliability. In healthcare, standardizing patient care processes has led to more efficient treatment and improved patient outcomes. Similarly, in construction, standardizing safety protocols has reduced workplace accidents and improved overall project efficiency.
Methodology for Standardizing Procedures
Standardization is an important part of the 5S Lean methodology at work. It means creating and following the same procedures to make manufacturing more consistent and efficient.
This might involve writing down procedures, training employees, and regularly checking that everyone sticks to the rules. For example, in manufacturing, standardization could mean labeling and storing tools in the same way and using the same kind of workstations to make things quicker.
By making procedures the same, companies can cut mistakes, waste, and boost productivity. Following the 5S system also means quality control is consistent, for example by testing products in the same way every time.
Examples of Effective Standardization
Organizations have implemented the 5S methodology to standardize procedures and streamline operations.
For example, manufacturing companies use visual controls and labeled workstations to ensure consistent processes and improve work efficiency. In healthcare, organizing medical supplies and standardizing cleaning procedures has led to improved patient care and reduced waiting times. Construction companies have also utilized the 5S framework by standardizing project management processes and equipment storage, resulting in enhanced project delivery times and improved safety practices. Standardization has contributed to overall efficiency and productivity by reducing waste, improving work environment safety, and enhancing work quality. This has also led to streamlined operations, enhanced employee morale, and greater customer satisfaction.
Step 5: Sustain (Shitsuke)
Interpreting the Need for Sustain in the 5S Process
The sustain step in the 5S process is important. It ensures that the improvements in workplace organization and efficiency are maintained over time.
Without ongoing efforts to sustain the changes, there is a risk of reverting to previous habits and inefficiencies. This undermines the original goals of the 5S process.
Some tactics for maintaining 5S standards over time include:
- Regular audits and inspections
- Ongoing employee training and engagement
- Visual management tools such as signs and labels
- Clear responsibilities for maintaining the 5S system.
Successful sustain initiatives in a work environment include:
- Regular 5S audits and Gemba walks to ensure continued adherence to standards
- Employee recognition programs for ongoing 5S compliance
- Integration of 5S into daily work routines and practices to make it a natural part of the workplace culture.
Tactics for Maintaining 5S Standards Overtime
To keep 5S standards in the workplace, it’s important to do regular training and refresher courses. These help reinforce the Sort, Set in Order, Shine, Standardize, and Sustain principles.
Visual tools like color-coded workstations, floor markings, and signs can also help sustain 5S practices. Regular audits and inspections help find areas for improvement and ensure that employees keep following the standards long-term.
Some successful initiatives for sustaining 5S standards include daily team huddles to discuss progress, rewarding employees who stick to 5S practices, and having a steering committee to oversee 5S standards.
These tactics help maintain an organized, efficient, and safe work environment for employees.
Authentic Examples of Sustain Initiatives
Successful sustain initiatives in the 5S implementation involve:
- Continuous monitoring.
- Regular audits.
- Employee engagement.
Organizations can maintain 5S standards by:
- Incorporating sustainment goals into the company’s overall strategy.
- Conducting frequent training sessions to reinforce the importance of the 5S principles.
For instance:
- A manufacturing plant can implement a daily walkthrough inspection to ensure adherence to 5S standards.
- A healthcare facility can involve staff in regular improvement events and recognition programs.
By consistently reinforcing the 5S principles and integrating them into the organizational culture, companies can successfully sustain the 5S process in the workplace environment.
Ensuring a Safe Work Environment with 5S Implementation
Implementing the 5S system helps create a safe work environment. It promotes a clean and organized workplace.
The first step, Sort, involves removing unnecessary items, reducing clutter, and eliminating safety hazards. This reduces the risk of accidents and injuries.
The Shine step focuses on cleanliness, preventing slips, trips, and falls.
The Set in Order and Standardize steps play a vital role in maintaining workplace safety. They establish designated storage, mark walkways, and promote safety awareness through visual controls.
Best practices for safety include regular inspections, involving employees in hazard identification, providing safety training, and integrating safety into 5S action plans.
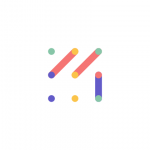
Vizologi is a revolutionary AI-generated business strategy tool that offers its users access to advanced features to create and refine start-up ideas quickly.
It generates limitless business ideas, gains insights on markets and competitors, and automates business plan creation.