Key Steps for Kaizen Improvement
The Japanese philosophy of Kaizen offers a powerful approach for continuous improvement. It focuses on small, incremental changes and has revolutionized businesses and organizations globally.
This article explores key steps for implementing Kaizen improvement. It covers establishing a culture of continuous improvement and empowering employees at all levels.
Understanding these fundamental principles can help unlock the full potential of Kaizen and drive lasting change within your organization.
Understanding the Kaizen Philosophy
Kaizen has core principles: management commitment, employee empowerment, and gemba walks. These principles promote continuous improvement by fostering collaboration and innovation.
Management commitment ensures resources are allocated for improvement, while employee empowerment encourages staff to contribute improvement suggestions.
Gemba walks, where leaders observe processes and engage with employees in the work area, are crucial for gaining insight into process efficiency and identifying improvement opportunities.
Kaizen gives organizations a competitive edge by continuously optimizing operations, improving work quality, and reducing waste.
However, potential drawbacks of implementing Kaizen include employee resistance to change, the need for sustained commitment from leadership and the workforce, and the challenge of balancing short-term gains with long-term improvement goals.
The Evolution of Kaizen
Kaizen has evolved over time. It started in post-World War II Japan and became a global management method in the 1980s. Masaaki Imai popularized it.
Kaizen has changed to meet the needs of modern businesses. It now focuses on management commitment, employee empowerment, and understanding process efficiency through gemba walks.
Several factors have influenced the development of Kaizen philosophy and principles. These include integrating with Standardized Work, capturing best practices, and promoting continuous improvement culture.
The Kaizen process now emphasizes long-term commitment to achieving operational excellence, improved work quality, and sustainable success through the PDCA cycle (Plan, Do, Check, Act).
Defining the Core Principles of Kaizen
Commitment from Management
Management shows its commitment to Kaizen by prioritizing long-term engagement and support for the methodology. This encourages a culture of Kaizen in the workplace.
They empower employees to make improvement suggestions and conduct gemba walks to understand process efficiency. They also support Kaizen blitz events to address process management and quality issues.
Furthermore, management actively participates in and champions the implementation of Kaizen initiatives by asking the right questions, performing root-cause analysis, and providing necessary support and resources to achieve significant results.
By embracing Kaizen, management plays a crucial role in fostering operational excellence, enhancing work quality, and driving sustainable success within the organization.
Empowering Employees
Kaizen is a management methodology focused on continuous improvement. It originated in post-World War II Japan and was later spread globally by Masaaki Imai in the 1980s. The key elements and core principles of kaizen include management commitment, employee empowerment, gemba walk, and the 5S principles.
To implement kaizen successfully, organizations should:
- Prioritize long-term commitment
- Empower employees to contribute improvement suggestions
- Conduct gemba walks to understand process efficiency
The process involves:
- Asking the right questions
- Performing root-cause analysis
- Conducting kaizen blitz events to achieve significant results in process management and quality issues.
Embracing kaizen leads to:
- Operational excellence
- Improved work quality
- Sustainable success
The Importance of Gemba Walks
Gemba walks play a crucial role in fostering a culture of continuous improvement within an organization. By physically going to the place where the work is done, managers can gain a deeper understanding of the processes, identify inefficiencies, and engage with frontline employees. Gemba walks contribute to empowering frontline employees by demonstrating that their work is valued, and by promoting a sense of accountability in the workplace.
By experiencing the work environment first-hand, managers can gain insights into the daily challenges faced by employees, which in turn can lead to more effective problem-solving and decision-making. Gemba walks help in identifying opportunities for process optimization and waste reduction within the organization by providing managers with a direct view of how work is being done. This can lead to more targeted improvements and the ability to address issues at the source, rather than applying band-aid solutions.
By involving everyone in the improvement process, Gemba walks contribute to a more efficient, effective, and engaged workforce.
Implementing the 5S System in Kaizen
The 5S System drives continuous improvement in the workplace. It integrates with the Kaizen philosophy to create an organized and efficient work environment. The key steps involved in implementing the 5S System within the Kaizen process are:
- Sort.
- Set in Order.
- Shine.
- Standardize.
- Sustain
These steps can be customized to fit the organization’s specific needs.
This involves employees at all levels, providing training on 5S principles and using visual management tools to sustain the improvements.
The implementation of the 5S System in Kaizen empowers employees. It gives them the responsibility to maintain a clean and organized workspace. This fosters a culture of continuous improvement, promoting teamwork, engagement, and ownership of the work environment.
This approach also encourages employees to identify and resolve problems. This leads to increased productivity and quality outcomes in the organization.
Step-by-Step Guide to the Kaizen Process
Kaizen has key elements and core principles. These include management commitment, employee empowerment, gemba walk, and the 5S principles. Implementing kaizen successfully requires long-term commitment, empowering employees to suggest improvements, and conducting gemba walks for process efficiency. The process involves asking the right questions, root-cause analysis, and kaizen blitz events for significant results.
Embracing kaizen leads to operational excellence, improved work quality, and sustainable success.
Initiating Kaizen for Organizational Growth
Embarking on the Kaizen Journey: A 5-Day Plan
Embarking on the Kaizen journey through a 5-day plan is a way for individuals and organizations to start making continuous improvements. This plan offers a structured approach to making small, ongoing changes that lead to significant improvements over time. By setting aside dedicated time and resources for 5 days, participants can fully immerse themselves in Kaizen principles and methodologies, laying the foundation for ongoing progress.
A successful 5-day Kaizen plan involves integrating key components such as management commitment, employee empowerment, and the gemba walk into daily activities and workshops. Through carefully designed exercises and activities, participants learn to spot improvement opportunities, create solutions, and implement changes effectively. The plan also includes the 5S principles to ensure that the workplace is organized, clean, and conducive to continuous improvement.
While engaging in the Kaizen journey with a 5-day plan, potential challenges may arise, such as resistance to change, lack of employee engagement, and difficulty sustaining improvements. These challenges can be addressed through effective communication, providing opportunities for employee input and involvement, and implementing regular follow-ups to track progress and address any emerging issues.
Crafting a Custom Kaizen Performance Checklist
A custom Kaizen performance checklist should include key performance indicators. These include process cycle time, defect rate, overall equipment effectiveness, and employee engagement.
This will let the organization measure and track improvements over time.
To tailor the checklist to the specific needs and goals, it’s important to involve employees at all levels. This can ensure that it reflects the unique challenges and opportunities within the company.
Incorporating the 5S framework and gemba walks into the checklist can provide a structured approach to improving workplace organization and identifying opportunities for process optimization.
Organizations can implement strategies such as regular training and workshops on using the checklist. They can also establish clear accountability for checklist implementation and reviews. They should foster a culture of continuous improvement where employees are encouraged to provide feedback and suggest updates to the checklist.
Diverse Types of Kaizen Initiatives
There are different types of Kaizen initiatives that can be used in an organization:
- The 5S framework focuses on organizing the workplace for efficiency and effectiveness.
- Gemba walks involve managers going to the actual workplace to observe, understand, and identify improvement opportunities.
- Kaizen blitz events are intensive and focused improvement projects aimed at achieving rapid results in a short period of time.
These diverse types of Kaizen initiatives contribute to continuous improvement in the workplace by:
- Promoting employee involvement
- Standardizing processes
- Eliminating waste
- Identifying and solving problems at their root causes.
Organizations benefit from implementing various types of Kaizen initiatives:
- Improving operational excellence
- Increasing work quality
- Fostering a culture of continuous improvement
- Achieving sustainable success.
Additionally, the implementation of Kaizen initiatives empowers employees to contribute improvement suggestions, leading to a greater sense of ownership and commitment to the company’s goals.
Exploring the Advantages and Challenges of Kaizen
How Kaizen Offers Competitive Edge
Kaizen offers specific strategies and tools. These can provide a competitive edge in the marketplace. One example is the 5S framework. Another is the cycle of Plan, Do, Check, and Act (PDCA).
By focusing on continuous improvement, Kaizen gives organizations an advantage. It allows them to constantly identify issues, create solutions, and implement improvements. This helps organizations stay ahead in a competitive business environment.
To effectively leverage the principles of Kaizen, organizations should prioritize long-term commitment. They should also empower employees to contribute improvement suggestions. Additionally, conducting gemba walks to understand process efficiency is important.
Embracing Kaizen ultimately leads to operational excellence, improved work quality, and sustainable success in the marketplace.
Potential Drawbacks and Mitigation Strategies
Potential drawbacks of implementing Kaizen in an organization may include resistance to change from employees, lack of standardized processes, and the risk of complacency due to incremental improvements.
To mitigate these drawbacks, organizations can implement strategies such as:
- conducting thorough change management training to address employee resistance,
- documenting and standardizing processes to ensure consistency,
- setting stretch goals to prevent complacency.
Additional strategies may include involving employees in the decision-making process, providing regular feedback and recognition for improvements, and creating a culture of continuous learning to ensure the successful adoption of Kaizen for sustained benefits in the organization.
By prioritizing employee engagement and a commitment to ongoing improvement, organizations can effectively overcome challenges associated with implementing Kaizen and create a culture that embraces continuous improvement for long-term success.
Real-World Success Stories of Kaizen Implementation
Organizations successfully incorporated Kaizen principles into their operations. They prioritized long-term commitment, empowered employees to contribute improvement suggestions, and conducted gemba walks to understand process efficiency.
They also implemented the 5S principles and conducted kaizen blitz events to achieve significant results in process management and quality issues. The implementation of Kaizen led to measurable improvements in productivity, efficiency, and overall business performance for these organizations.
It contributed to operational excellence, improved work quality, and sustainable success. Some key challenges faced during the Kaizen implementation process included resistance to change, lack of employee engagement, and difficulty in maintaining momentum.
These challenges were overcome through effective communication, continuous training and coaching, and establishing a culture of continuous improvement. Real-world scenarios have demonstrated tangible results in the form of streamlined processes, reduced waste, increased employee morale, and enhanced customer satisfaction as a result of successful Kaizen implementation.
Adopting Continuous Improvement in the Workplace
Management can show commitment to continuous improvement by prioritizing long-term dedication to the process. They can set an example for employees by consistently endorsing and participating in the Kaizen approach. Gemba walks empower employees to join in improvement initiatives. This involves managers observing the work environment and interacting with employees to understand process efficiency.
The benefits of adopting Kaizen include operational excellence, improved work quality, and sustainable success. However, there are challenges such as the need for employee empowerment and conducting kaizen blitz events for significant results.
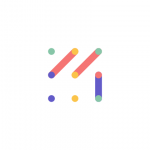
Vizologi is a revolutionary AI-generated business strategy tool that offers its users access to advanced features to create and refine start-up ideas quickly.
It generates limitless business ideas, gains insights on markets and competitors, and automates business plan creation.