Main Principles of Lean Management
Lean management is a great way to make businesses better. It focuses on using resources wisely and making sure things are valuable. This helps companies make better products, save money, and improve their services.
We’ll look at the main principles of lean management in this article. These principles can be used to succeed in today’s tough business world. No matter what industry you’re in, knowing these principles can really help your business do better.
Essential Concepts of Lean Improvement
Defining Lean Process Enhancement
Lean process enhancement is a management approach that focuses on identifying and eliminating waste, improving efficiency, and increasing value for the customer. It emphasizes continuous improvement and strongly considers the customer’s perspective.
The core concepts of Lean methodology are:
- Process Is Primary.
- Grasping Reality Improves Processes.
- Visual Communication Is Central
These concepts contribute to process improvement by shifting the focus from results to processes, monitoring real-time performance, and enhancing communication within the organization.
By prioritizing the customer’s perspective, Lean methodology aligns processes to create value, identifies and eliminates non-value-adding activities, and enhances the overall customer experience.
Core Concepts Underpinning Lean Methodology
The value stream is important in Lean methodology. It helps organizations identify and eliminate activities that do not add value from the customer’s perspective. This involves mapping out every step of the process, from raw materials to the delivery of the final product or service. The goal is to streamline the flow of value and eliminate waste.
Pursuing perfection in processes is essential in Lean methodology. It encourages organizations to continuously improve and optimize their operations. This involves seeking out and eliminating any inefficiencies, defects, or non-value adding activities in the process to achieve the highest level of quality and efficiency.
In Lean management systems, the critical roles include effective management, real-time monitoring, and visual communication. These roles contribute to the core concepts of Lean methodology by ensuring that processes are the primary focus, reality is accurately understood and used to improve processes, and important information is communicated visually to all stakeholders for better decision-making and problem-solving.
Value from the Customer’s Perspective
The organization focuses on delivering value from the customer’s perspective. This means getting rid of waste and always trying to do better. If something doesn’t add value for the customer, it’s considered a waste. The organization uses processes like real-time monitoring and good communication to make sure they’re always thinking about the customer.
They also believe that focusing on processes, understanding what’s really going on in those processes, and using visuals to communicate are really important. They measure success by finding problems, delivering value to customers, and always trying to get better. This helps them improve quality, efficiency, and how much money they make.
The Value Stream and its Importance
The value stream is important in Lean methodology. It helps organizations identify and eliminate wasteful activities, improving the flow of value to customers. Understanding the value stream contributes to process improvement. It provides insights into how value is created and delivered, allowing for targeted efforts to streamline and optimize these processes.
Optimizing the value stream has a significant impact on organizational efficiency and effectiveness, reducing lead times, increasing productivity, and minimizing costs. This leads to improved customer satisfaction, increased competitiveness, and ultimately, higher profitability for the organization.
The Flows in Lean: Creating Smooth Process Flows
Creating smooth process flows in Lean management involves three key principles:
- Process Is Primary: Focus on efficient processes rather than solely on outcomes. This helps identify and eliminate waste, reduce lead times, and enhance overall quality.
- Grasping Reality Improves Processes: Real-time monitoring and deep understanding of the current state drive continuous improvement.
- Visual Communication Is Central: Transparent and effective communication promotes collaboration and problem-solving.
Strategies like value stream mapping, pull systems, and aligning team members with a shared vision of success optimize and create smooth process flows in a Lean environment. These principles and strategies are important for achieving improved quality, efficiency, and profitability in Lean management.
The Pursuit of Perfection in Processes
The pursuit of perfection in processes aligns with lean management. Lean principles focus on continuous improvement and waste reduction to achieve efficiency and effectiveness.
Lean principles aim to eliminate activities that do not add value to the customer, striving for perfection in processes. Continual improvement is crucial, requiring organizations to analyze and refine processes to enhance quality, efficiency, and profitability.
By embracing continuous improvement, organizations can measure success through key performance indicators, such as reduced lead times, increased productivity, and improved customer satisfaction.
Lean management principles provide a framework for organizations to evaluate their progress and guide them toward sustained success and competitive advantage.
Comparing Lean to Alternative Management Approaches
The value stream in Lean methodology focuses on identifying and eliminating waste in the entire process of delivering a product or service. This is different from other management approaches that focus on individual activities. Lean aims to optimize the flow of value to the customer, leading to increased efficiency and reduced costs.
Lean’s pursuit of perfection emphasizes continuous improvement rather than a one-time fix. It prioritizes the idea that processes can always be improved, framing perfection as a journey rather than a destination. This sets Lean apart from management approaches that focus on achieving a predetermined ideal state and then maintaining it.
In Lean management, continual improvement and Kaizen are intentional and ongoing. It encourages a culture of continuous improvement at all levels of an organization, while other management approaches may only address improvements on an as-needed basis or during specific improvement initiatives. This commitment to constant incremental progress sets Lean apart and can result in more sustainable and lasting improvements.
Critical Roles in Lean Management Systems
In Lean management systems, leadership, employee engagement, and performance measurement play important roles in the success of lean initiatives.
Leadership shapes the Lean culture by promoting continuous improvement and supporting innovation and change.
Employee engagement creates a sense of ownership and responsibility, increasing motivation and productivity.
Key metrics like cycle time, lead time, defect rate, and overall equipment effectiveness (OEE) measure the effectiveness of Lean management in terms of quality, efficiency, and profitability.
Focusing on these roles and using key metrics helps organizations achieve sustainable improvements and remain competitive in today’s business environment.
Eliminating Waste: The Heart of Lean Principles
Types of Waste in Lean Theory
There are different types of waste in Lean Theory. Defects, overproduction, waiting, non-utilized talent, transportation, inventory excess, motion waste, and extra processing are some examples.
Defects can impact quality and cost, leading to rework, customer complaints, and increased expenses.
Inventory surpluses and unnecessary movements of people or information can contribute to inefficiencies, increased lead times, and extra costs. By identifying and eliminating these types of waste, organizations can improve quality, streamline processes, and reduce operational costs. This leads to increased efficiency and profitability.
Defects Impacting Quality and Cost
Defects in the production process, like rework or errors, can have a big impact on quality and production cost. They often lead to more waste, higher costs, and lower customer satisfaction.
For example, defects might mean needing extra materials or resources to fix errors, which increases expenses. Also, defects can cause production delays, missed deadlines, and potential penalties.
Lean management systems focus on finding and fixing defects through ongoing improvement. Strategies like real-time monitoring, root cause analysis, and visual communication help organizations identify and address production defects. For instance, tools like Kanban boards and Andon systems allow teams to quickly spot and fix defects as they happen, improving quality and lowering costs. Also, creating a culture of continuous improvement and encouraging employees to actively take part in defect identification and resolution is key to enhancing quality and cutting costs in a lean management system.
Excess Processing: A Hidden Source of Waste
Excess processing can lead to waste in a lean management system. This happens when resources are used for activities that don’t add value.
For example, adding unnecessary steps in a production process or over-engineering a product can increase costs and waste time. This goes against the core principle of Lean management, which is to provide value to the customer.
Excess processing can decrease productivity, increase lead times, and lower overall quality. It can also harm organizational agility and flexibility. To tackle this, organizations should closely examine their processes to identify non-value adding activities. Using visual management tools and involving employees in problem-solving can help streamline processes and optimize resource use.
Additionally, benchmarking and performance metrics can identify areas for improvement, bringing the organization closer to its Lean objectives.
Inventory Surpluses and Waste
Lean principles help organizations identify and address inventory surpluses through process improvement and value delivery. Using Lean management, companies can implement strategies like just-in-time inventory, visual management, and kanban systems to minimize waste. Prioritizing value and efficiency, Lean principles can reduce inventory surpluses and waste.
For instance, a company can use Lean thinking to identify excess inventory and eliminate non-value adding activities in production, leading to improved inventory turnover and reduced carrying costs.
Unnecessary Movement of People or Information
Unnecessary movement of people in a lean process can be excessive walking, searching for tools or materials, or waiting due to poor layout or lack of standardization. For example, a worker may have to walk back and forth between different workstations, resulting in wasted time and energy.
Similarly, unnecessary movement of information can lead to inefficiency in a lean system. This can happen when documents or data are not readily accessible, causing delays in decision-making and problem-solving.
In a lean environment, timely access to accurate information is important for identifying and addressing process inefficiencies.
Continual Improvement: Kaizen in Lean Management
Practicing Kaizen: Small, Incremental Changes
Small, incremental changes are key to practicing Kaizen in Lean management. Encouraging employees to identify and address small inefficiencies in their daily work processes empowers teams to make decisions and drive improvements. This creates a culture of continuous improvement through Kaizen.
Success in Lean initiatives can be measured by tracking the impact on quality, efficiency, and customer satisfaction when implementing small, incremental changes through Kaizen. Real-time monitoring and regular feedback loops ensure that improvements align with organizational goals and customer needs.
Focusing on the process, integrating visual management and communication tools, and understanding operational workflows are essential for effective Kaizen practices. This approach helps organizations achieve sustainable improvements in their operations.
Empowering Teams to Drive Improvements
Teams can drive improvements within lean management by focusing on three key principles:
- Process Is Primary.
- Grasping Reality Improves Processes.
- Visual Communication Is Central.
By prioritizing the process over results, teams can identify and eliminate waste, leading to improved efficiency and customer value.
Strategies to encourage employee engagement in lean transformations and continual improvement initiatives include:
- Real-time monitoring
- Effective communication
- Use of a pull system to identify and address inefficiencies.
Leadership can shape a lean culture within an organization by providing support, resources, and training to enable successful implementation of Lean practices, ultimately driving improvements in quality, efficiency, and profitability.
The Importance of Flexibility and Adaptability
Flexibility and adaptability are essential for the success of lean management systems. They allow for quick and efficient responses to changing conditions, both internal and external. An organization that is adaptable can easily adjust its processes to meet customer demands and maximize efficiency, reducing waste. Embracing change and new technologies is another way to demonstrate the importance of flexibility and adaptability in lean principles.
This helps organizations remain competitive and continuously improve their processes to deliver greater value to customers. Flexibility and adaptability also play a significant role in creating a lean culture by fostering an environment that encourages experimentation, problem-solving, and innovative thinking. This, in turn, facilitates the identification and elimination of waste, as well as the promotion of continuous improvement, which are fundamental aspects of lean management principles.
Building a Lean Culture Within an Organization
Leadership’s Role in Shaping Lean Culture
Effective leadership is important for developing a lean culture in an organization. Leaders influence employees’ mindset and behavior by promoting waste elimination, continuous improvement, and three key lean management principles. They also foster accountability, collaboration, and a learning environment that values innovation and problem-solving.
Leadership aligns the organization’s goals with lean principles, empowers employees to make data-driven decisions, and creates a work environment that encourages experimentation and incremental improvements.
Employee Engagement in Lean Transformations
Organizations can help employees get involved in lean transformations by encouraging open communication and feedback. This includes involving them in decision-making and empowering them to share ideas for improvement. Engaging employees in this way creates a culture of continuous improvement and boosts operational efficiency. When employees feel valued and engaged, they are more likely to embrace change, identify inefficiencies, and contribute to the success of lean initiatives.
This ultimatelydrives value for customers and reduces business costs.
Measuring Success in Lean Initiatives
Measuring the success of Lean initiatives involves using key performance indicators (KPIs) to evaluate different parts of the process.
For example, KPIs can include metrics like cycle time, lead time, and on-time delivery. These give measurable data on process efficiency and customer satisfaction.
Organizations can also measure Lean success by including customer satisfaction and feedback. This can be done through feedback systems and customer surveys to understand the impact of Lean improvements on overall satisfaction and loyalty.
Additionally, organizations track and assess the impact of Lean improvements on productivity and efficiency. They do this by analyzing data on resource utilization, defect rates, and overall operational costs.
This helps them identify areas for improvement and measure the concrete impact of Lean practices on the organization’s operational performance.
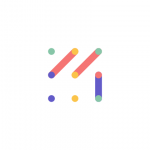
Vizologi is a revolutionary AI-generated business strategy tool that offers its users access to advanced features to create and refine start-up ideas quickly.
It generates limitless business ideas, gains insights on markets and competitors, and automates business plan creation.