Streamlining Work: Lean Methodology and Automation
In today’s fast-paced business environment, companies want to streamline work processes and increase efficiency. Lean methodology and automation are effective strategies to achieve this goal.
Lean methodology focuses on eliminating waste and optimizing workflows, helping businesses operate more efficiently.
Automation technology allows for faster completion of repetitive tasks with fewer errors.
These methods can significantly improve productivity and ultimately lead to cost savings for organizations.
Understanding Lean Automation
Defining Lean Automation and Its Core Objectives
Lean Automation is a method that combines Lean six sigma with business process automation. It focuses on reducing waste in business processes before automating tasks. The goal is to enable the adoption of business technology through iterative improvements rather than overall transformations.
Lean Automation differs from traditional methods by gradually automating processes. This results in faster and more efficient production facilities, waste elimination, Internet of Things integration, cost management, improved security, accuracy, and maximized productivity.
The main objectives of implementing Lean Automation are to increase worker safety, reduce lead times, improve accuracy, and cut costs. Additionally, the approach ensures proper workflow setup, evenly distributed responsibility, open communication with employees, and adequate training.
Comparing Traditional Automation and Lean Automation
The way traditional automation and lean automation differ is in their approach. Traditional automation focuses on complete transformations when delivering business software. On the other hand, lean automation emphasizes iterative improvements before automating tasks.
When it comes to impact, traditional automation has minimal focus on process reconfiguration, worker safety, lead times, accuracy, and operational costs. In comparison, lean automation takes into account these key aspects of production, leading to reduced waste and improved productivity.
Lean automation is effective in identifying and addressing inefficiencies in processes before implementation. It utilizes Lean principles to gradually automate processes, ensuring faster and more efficient production facilities.
This approach enables companies to carefully examine their existing business processes and obtain a clear understanding of the new processes they want business process automation to enable before implementing any technology.
The implementation of lean automation has proven to increase worker safety, reduce lead times, improve accuracy, and cut operational costs.
Advantages of Integrating Lean Methodology with Automation
Increase in Worker Safety
Implementing Lean Automation in manufacturing processes can enhance worker safety. It reduces human intervention in repetitive and hazardous tasks, like manual material handling and exposure to harmful substances. Technology and automation streamline production processes, minimizing the risk of accidents linked to human error.
Companies can rearrange workspaces and production lines using Lean principles to lower the risk of workplace injuries. To boost worker safety, they can invest in automated equipment with built-in safety features and sensors, reducing physical strain and exposure to dangerous machinery. Employee training on safe use of automated systems and adherence to standardized operating procedures is also essential.
Lean Automation simplifies production processes, eliminating manual tasks and reducing reliance on human involvement. This minimizes the risks of accidents and occupational hazards. The integration of automation also allows for advanced safety protocols, the use of smart sensors to detect hazards, and the creation of safety-focused work environments.
Reduction of Lead Times
Reducing lead times in manufacturing or service environments involves integrating lean methodology with automation. Lean principles, when combined with gradual automation, lead to faster and more efficient production.
When choosing business process automation tools, organizations focus on “Ability to Execute” and “Completeness of Vision.”
However, integrating lean methodology with automation can face barriers. Without reconfiguring processes and the management team’s support, the benefits may be minimal or non-existent. Therefore, it’s crucial to evaluate the time and cost involved in manual tasks versus automated tasks before implementing lean automation.
Despite these challenges, lean automation offers manifold benefits and significantly reduces lead times in manufacturing or service environments.
Enhancement of Accuracy and Precision
Lean methodology, when combined with automation, helps improve processes gradually by eliminating waste and errors. This results in higher accuracy and precision. It focuses on making iterative improvements and reducing inefficiencies. This leads to better product quality and fewer errors in manufacturing.
To ensure accuracy and precision with lean automation, it’s important to thoroughly examine current business processes. Reconfiguring processes, teams, and organizations is also crucial. Choosing the right business process automation tools is key. Open communication with employees, fair distribution of responsibility, and effective technology training are also important. Taking these steps can help organizations achieve enhanced accuracy and precision through lean automation.
Lowering Operational Costs
Companies can improve their operational processes by first examining their current business processes and the processes they want Business Process Automation (BPA) to support. It’s important to understand both the existing processes and how new ones can be enabled before implementing any technology.
Integrating lean methodology with automation can help cut operational costs by reducing waste in executing business processes before automating tasks. This approach involves making iterative improvements, leading to faster and more efficient production facilities.
To calculate the return on investment for lean automation initiatives, consider the TIME spent on manual tasks, frequency of tasks per month, cost per hour, and yearly costs of manual tasks. This calculation helps build the financial case for implementation. By understanding lean automation, companies can achieve a 5X return on investment, simplifying maintenance, managing data, and improving reporting.
Identifying Inefficiencies Prior to Automation
The Dangers of Automating Ineffective Processes
Automating ineffective processes can be unhelpful for businesses. This is because it just makes the inefficiency faster without fixing the real problem. While it might save some money, it misses chances to make processes better and cheaper. To avoid these problems, organizations should first understand their current processes and figure out what new processes they want automation to help with.
They should also change their processes and teams, and think about Lean methods to improve data management and reporting. One way to reduce the risks of automating ineffective processes is to take time to think about how processes, teams, and organizations can be changed to make automation work. This way, automation won’t just do processes faster, but also make them better.
How to Evaluate Processes Before Implementing Automation
When evaluating processes before deciding to implement automation, companies should consider how each process can be reconfigured or improved to pave the way for automation. This may involve a detailed analysis and potential redesign of the processes, teams, and even the organization to ensure that they are suitable for automation.
Additionally, organizations should consider the ability of the automation technologies to execute the required tasks and have a complete vision of how the automation process will function. Identifying and mitigating the potential dangers of automating ineffective processes before implementation involves a methodical approach to the evaluation of the current processes.
Utilizing lean thinking can help reduce development times, simplify maintenance, reduce the gap between people and machines, and improve data management and reporting. Thoroughly assessing current processes to determine their suitability for automation can involve evaluating tools based on the criteria of the ability to execute and the completeness of vision.
Using a basic ROI calculation approach can also help in determining whether automation is suited for a particular process by considering the time spent on manual tasks, frequency of performing tasks, and the associated costs.
Implementing Lean Automation
Assessing Current Processes
LEAN methodology helps to measure and evaluate current processes for efficiency and effectiveness. It does this by identifying waste and inefficiencies. Key performance indicators used to assess the current processes include lead time, defect rates, cycle times, and process time.
Before implementing automation, potential areas for improvement in the current processes may include reducing unnecessary steps, improving communication, and standardizing procedures.
Lean Automation focuses on continually improving processes to optimize productivity and quality, and then automates tasks.
Analyzing Human Resource Implications
Implementing lean automation will have a big impact on the current workforce. As automation takes over some tasks, employees will need to adjust to new responsibilities. This may mean needing more training and professional development to stay relevant in their roles.
To assess the human resource implications of implementing lean automation, some strategies can be used. These include evaluating the workforce to find any skill gaps, setting up programs to transfer knowledge so that employees can handle new technologies, and providing ongoing support and mentorship to help with the transition.
Challenges of implementing lean automation can be reduced by communicating clearly and using transparent change management strategies. The organization should highlight the importance of effective training and development programs to make sure the workforce can successfully bring in lean automation. This might mean training in new technologies, data management, and analytics, as well as change management and continuous improvement initiatives to keep operations running smoothly.
Selecting Appropriate Tools and Technologies
When selecting tools and technologies for automation processes, it’s important to consider:
- Ability to execute and completeness of vision
- Factors such as scalability, adaptability, and user-friendliness
- Predicted ability to deliver desired automation outcomes
Integrating lean methodology can also impact the selection process as it emphasizes iterative improvements over overall transformations. This approach aligns technology with gradual business process streamlining, leading to more effective automation.
Financial benefits of selecting appropriate tools for lean automation initiatives may include:
- Reduction in manual task costs
- Increased productivity
- Improved data management and reporting
- Positive return on investment
By choosing tools that align with lean principles, companies can avoid automating inefficient processes, resulting in significant cost savings and process improvements.
Strategic Roadmap for Lean Automation Roll-out
Implementing lean automation involves integrating lean principles with gradual process automation to enhance production efficiency and reduce costs. To do this, the organization can assess current processes and analyze human resource implications by applying Lean thinking. This can help reduce development times, simplify maintenance, bridge the gap between people and machines, and improve data management, reporting, and training.
To calculate the financial case for lean automation ROI, the organization can multiply the time spent on manual tasks, frequency of performing tasks per month, and the cost per hour. Then, deduct the total yearly costs of manual tasks.
Additionally, the organization can evaluate business automation tools based on their ability to execute and completeness of vision.
Lean Automation ROI: Making the Financial Case
Calculating Return on Investment for Lean Automation Initiatives
Calculating the return on investment for lean automation initiatives involves considering factors such as time spent on manual tasks, task frequency, and cost per hour. By comparing yearly costs of manual tasks with automation tool costs, financial benefits can be accurately measured. Methodologies and tools for determining the return on investment include assessing time spent on manual tasks, task frequency, and identifying associated costs.
Evaluating specific business process automation tools should also consider the ability to execute and vision completeness.
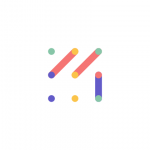
Vizologi is a revolutionary AI-generated business strategy tool that offers its users access to advanced features to create and refine start-up ideas quickly.
It generates limitless business ideas, gains insights on markets and competitors, and automates business plan creation.