What Makes Toyota’s Car Making Different?
Toyota is known for their exceptional car making process. They stand out in the industry due to their innovative production methods and strong focus on quality and efficiency. This unique approach has shaped Toyota’s reputation for reliability and excellence in the competitive automobile manufacturing world.
Inception of Toyota’s Unique Approach to Car Manufacturing
Toyota’s production methods are unique because of Jidoka and Just-In-Time. These concepts aim to eliminate waste, achieve high efficiency, and make work easier for workers. They focus on creating meaningful work.
Using these concepts, Toyota produces products efficiently and at the pace of customer demand. This ensures high-quality standards and meets individual customer requirements for every vehicle.
They apply the Toyota Production System (TPS) to ensure manufacturing excellence. TPS emphasizes reaching operational excellence, continuous improvement, and involving all employees in the process.
The core principles of Toyota’s manufacturing excellence include eliminating unnecessary processes, maintaining high-quality standards, and continuously improving efficiency and productivity.
TPS has played a vital role in Toyota’s success, especially during supply chain disruptions, showcasing the company’s ability to outperform its rivals.
Underlying Concepts Shaping Toyota’s Production Methods
The Pursuit of Continuous Improvement
Toyota has been successful in the manufacturing industry due to its focus on continuous improvement. This includes eliminating waste, achieving high efficiency, and making work easier for its employees.
The concepts of Jidoka and Just-In-Time are key to Toyota’s approach to continually improving production methods. By applying these concepts, Toyota can produce its products efficiently and at the pace of customer demand, ensuring high-quality standards are met.
Toyota is committed to refining its methods and maintaining quality, safety, and efficiency in all aspects of production. This dedication has allowed Toyota to outperform its rivals and remain a leader in the manufacturing industry.
Adherence to Respect in the Workplace
At Toyota, respecting each other at work is really important. They make sure their employees are treated well by promoting open communication, listening, and feedback. This helps create a culture of teamwork and respect where everyone’s input matters. Toyota believes that by focusing on respect at work, they can create a better environment for their employees, leading to higher morale, productivity, and job satisfaction.
This connects with their Toyota Production System, which aims to make workeasier, meaningful, and efficient. Toyota’s commitment to respect not only builds a positive culture but also supports their goal of delivering great products and meeting customer needs.
Ensuring Excellence Through the Right Processes
The Toyota Production System ensures excellence through the right processes. It prioritizes meaningful work and efficiency, achieved through the core concepts of Jidoka and Just-In-Time. These enable the production of high-quality products aligned with customer demand. By focusing on making work easier for workers, Toyota’s approach eliminates waste and achieves high efficiency.
These core principles guide Toyota’s manufacturing excellence and contribute to ensuring the right processes by emphasizing quality standards and individual customer requirements. Furthermore, Toyota enhances organizational value through people development and root problem analysis for sustained organizational learning.
This consistent focus on people development and ongoing root problem analysis fosters a culture of continuous improvement, ultimately ensuring excellence through the right processes within the organization.
Core Principles Guiding Toyota’s Manufacturing Excellence
Enhancing Organizational Value Through People Development
The Toyota Production System focuses on enhancing organizational value through people development. This means investing in the skills and knowledge of the workforce to drive continuous improvement and innovation. By doing so, companies can achieve increased productivity, reduced waste, and higher quality standards, all contributing to organizational value.
Toyota’s emphasis on respect for people and creating meaningful work fosters a culture of continuous improvement and employee empowerment. Integrating these strategies into the organization encourages collaboration, creativity, and problem-solving among the workforce. Nurturing a culture of continuous improvement and respect in the workplace maximizes the potential of employees, ultimately enhancing organizational value. The TPS is a standout example of how investing in people development can sustain success and competitiveness in the industry.
Root Problem Analysis for Sustained Organizational Learning
Effective problem analysis and resolution are important for sustained organizational learning. The Toyota Production System is a recognized method for identifying root causes of organizational learning issues. Through concepts like Jidoka and Just-In-Time, organizations can achieve efficiency and reduce waste, making work easier for employees. Continuous improvement, a key part of TPS, plays a significant role in addressing and resolving root problems in organizational learning.
By continually refining processes and systems, organizations can better adapt to changes, fostering sustained organizational learning. Making work easier and more meaningful for workers creates an environment where employees can focus on quality standards and individual customer requirements. The TPS principles have proven to be successful in this regard, providing practical examples of its effectiveness.
Collaborative Efforts: Learning from Toyota’s Teamwork Ethos
Toyota’s teamwork ethos contributes to its success in car manufacturing. The company’s commitment to collaboration ensures that employees work together efficiently. Management practices such as regular team meetings and shared decision-making processes create an environment that facilitates teamwork. Toyota’s dedication to continuous improvement and respect in the workplace enhances its collaborative efforts.
Its utilization of the Toyota Production System focuses on eliminating waste and achieving high efficiency, making work easier for workers. By encouraging meaningful work and applying the concepts of Jidoka and Just-In-Time, Toyota produces high-quality products efficiently, meeting quality standards and individual customer requirements.
Management Practices Within Toyota’s Workspaces
Toyota’s management approach focuses on continuous improvement in workspaces. It emphasizes making work easier and less burdensome for workers. The Toyota Production System and concepts like Jidoka and Just-In-Time help workers produce products efficiently and at the pace of customer demand. This adherence to lean manufacturing eliminates waste and ensures high efficiency, meeting high-quality standards and individual customer requirements.
Respect in the workplace is crucial to Toyota’s management practices. The company prioritizes respect for people, providing workers with meaningful work and a sense of purpose. Through these practices, Toyota ensures excellence by continually refining processes, using the right tools, improving workflow, and working towards perfection in the workspaces.
Terminology Unique to Toyota’s Manufacturing Approach
The Toyota Production System is focused on reducing waste and achieving high efficiency. It emphasizes two concepts: Jidoka and Just-In-Time. Jidoka involves detecting problems and stopping production to address them promptly, ensuring quality and efficiency. Just-In-Time focuses on producing vehicles based on customer demand, reducing inventory costs, and accelerating the manufacturing process.
By following these concepts, Toyota streamlines its production methods, maintains high-quality standards, and meets individual customer requirements. This approach has contributed to the company’s success in car manufacturing by creating meaningful work and reducing the burden on workers.
Additionally, these concepts shape Toyota’s production and management practices by promoting worker empowerment, efficient resource allocation, and continuous improvement.
As a result, TPS has played a significant role in Toyota’s ability to outperform rivals and survive supply chain disruptions, showcasing the enduring relevance and effectiveness of the company’s manufacturing approach.
Additional Factors Contributing to Toyota’s Industrial Success
Toyota’s core principles and management practices are significant contributors to its manufacturing excellence. The Toyota Production System emphasizes eliminating waste and achieving high efficiency. It also focuses on making work easier and less burdensome for workers.
The concepts of Jidoka and Just-In-Time are at the heart of TPS, ensuring high-quality standards and meeting individual customer requirements. Continuous improvement, respect in the workplace, and a teamwork ethos also play a crucial role in Toyota’s industrial success.
By encouraging these values, Toyota ensures that its employees are empowered to contribute to the company’s overall success. This fosters sustained organizational learning and value through people development. This focus on ongoing learning and employee development is fundamental to Toyota’s industrial success, setting it apart from its competitors.
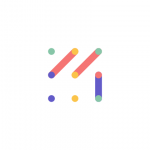
Vizologi is a revolutionary AI-generated business strategy tool that offers its users access to advanced features to create and refine start-up ideas quickly.
It generates limitless business ideas, gains insights on markets and competitors, and automates business plan creation.